e-Edu Library | Autonics 대한민국
Universal, Smart, Easy

공장이 스마트해지기 위해서는 가장 하위 필드에 위치한 센서까지 스마트해야 합니다.
IO-Link 통신이 가능한 센서의 경우, 다양한 데이터를 수집하여 상위기기에 전달하기 때문에
센서 상태에 대한 실시간 모니터링으로 예지보전 및 수명 관리 등이 가능해집니다.
IO-Link 통신이 가능한 센서의 경우, 다양한 데이터를 수집하여 상위기기에 전달하기 때문에
센서 상태에 대한 실시간 모니터링으로 예지보전 및 수명 관리 등이 가능해집니다.
이렇듯 IO-Link 통신은 센서의 정보화를 실현하며 유연성, 효율성을 필두로 하여
현장의 최적의 솔루션으로 거듭나고 있습니다.
현장의 최적의 솔루션으로 거듭나고 있습니다.
왜 IO-Link 통신인가

센서의 정보화
센서 레벨 내 모든
데이터 정보화 실현
데이터 정보화 실현

실시간 모니터링
실시간 상태 진단
및 예지보전
및 예지보전

양방향 통신
센서 레벨과 상위 레벨의
양방향 통신 가능
양방향 통신 가능

생산성 향상
제조 현장에 대한 피드백으로
생산성 및 품질 향상
생산성 및 품질 향상


모든 산업의 지향점인 스마트 팩토리, 이를 실현할 열쇠는 바로 IO-Link 통신입니다. 스마트팩토리
에서는 기존보다 많은 I/O 디바이스가 필요하고 해당 정보를 수집할 수 있는 통신이 필요합니다.
컨트롤러 레벨의 경우, 산업용 네트워크를 통하여 디바이스 통합이 가능하지만 센서 레벨에서는 디바이스 통합이 어려워 통신에 대한 필요성이 계속 제기되어 왔으며 주요 생산 방식이 다품종 소량 생산으로 변화됨에 따라 유동적인 생산 라인 대응에 대한 필요성 역시 강조되어 왔습니다. 이에 대해
많은 기업은 IO-Link 통신을 그 해답으로 채택하고 있습니다.
IO-Link 통신은 기존 설치된 ON/OFF 신호선을 이용하여 센서 레벨의 데이터를 수집해 공장 내 모든 기기와 장비를 연결할 수 있게 합니다. 그러므로 현장 데이터에 대한 실시간 모니터링과 예지보전을 실현할 수 있으며 설비의 다운타임을 줄일 수 있어 공장의 생산성 향상과 효율적인 장비의 운용을 실현
할 수 있습니다. 이것이 바로 기업들이 IO-Link 시스템을 도입하는 이유입니다.
IO-Link 통신이란
IO-Link 통신은 산업용 통신 네트워크 표준인 IEC 61131-9를 기반으로 하는 개방형 표준 직렬 프로토콜로 IO-Link 디바이스와 IO-Link 마스터 간에 양방향 정보 교환을
가능케 하는 통신 기술입니다. IO-Link 마스터를 통해 IO-Link 디바이스의 정보가 전달되기 때문에 센서 레벨의 데이터 통합으로 현장 전체를 효율적으로 관리할 수 있습니다.
가능케 하는 통신 기술입니다. IO-Link 마스터를 통해 IO-Link 디바이스의 정보가 전달되기 때문에 센서 레벨의 데이터 통합으로 현장 전체를 효율적으로 관리할 수 있습니다.
IO-Link 시스템 아키텍쳐

IO-Link 시스템 구성 요소

IO-Link Master
IO-Link Device와 상위 레벨간의 통신 게이트 웨이 역할을 수행합니다. IO-Link Master를 사용하면 하위기기 신호(IO-Link 통신, 일반 I/O)를 산업용 통신으로 교환할 수 있습니다.

IO-Link Device
IO-Link 통신을 지원하는 센서 레벨의 기기 입니다. 해당 디바이스는 IO-Link 마스터와 송수신 할 수 있으며 여러 데이터에 대한 설정도 가능합니다.

Software
IO-Link 제품의 설정 및 진단, 유지보수 등이 가능한 프로그램입니다. 해당 프로그램을 통해 IO-Link 디바이스의 각종 데이터를 확인할 수 있습니다.
IO-Link 통신의 이점
양방향 통신 가능
IO-Link 통신은 센서 레벨의 정보를 전달하여 상위 레벨과 양방향 통신을 가능하게 합니다. 실시간으로 모니터링되는 센서 레벨의 정보로
현장 운영의 용이함은 물론, 예지보전, 이상 감지 등에 대한 이슈도 제어할 수 있어 효율적인 생산 체계를 실현할 수 있습니다.
현장 운영의 용이함은 물론, 예지보전, 이상 감지 등에 대한 이슈도 제어할 수 있어 효율적인 생산 체계를 실현할 수 있습니다.
IO-Link 시스템
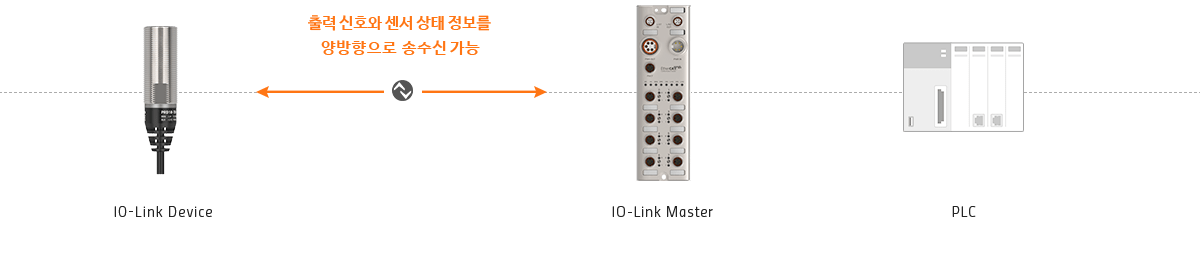
설계 및 설치의 간소화
IO-Link 통신은 센서의 출력 신호에 맞는 제어기기가 필요하지 않고 IO-Link 마스터로 표준화할 수 있습니다.
또한 IO-Link 통신은 ON/OFF 선과 통신선을 공용으로 사용하기 때문에 전용 통신 케이블이나 기본 3선/4선/5선의 비실드 케이블을 사용할 수 있습니다.
또한 IO-Link 통신은 ON/OFF 선과 통신선을 공용으로 사용하기 때문에 전용 통신 케이블이나 기본 3선/4선/5선의 비실드 케이블을 사용할 수 있습니다.
일반 시스템
센서의 출력 신호에 맞는 제어기기가 필요합니다.


IO-Link 시스템
센서에 맞는 제어기기가 필요하지 않으며
표준화된 결선으로 배선의 간편함을 실현할 수 있습니다.
표준화된 결선으로 배선의 간편함을 실현할 수 있습니다.
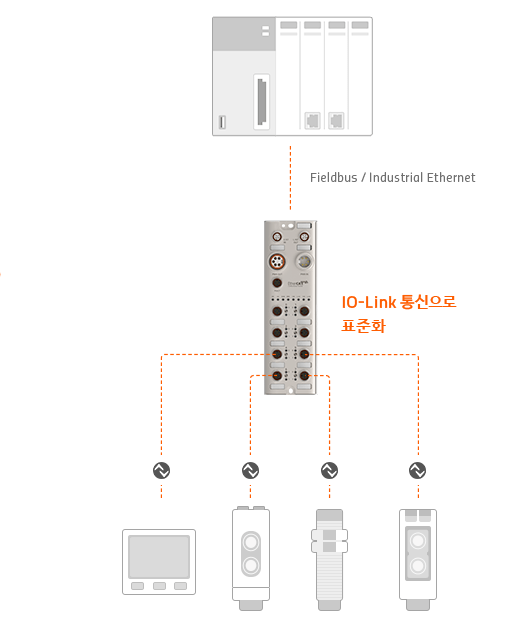
ID 식별로 이상 원인 및 빠른 복구
현장 라인에는 수천 개의 센서가 존재합니다. IO-Link 통신을 적용하면 SCADA 등에서 지정한 ID를 통해 이상 센서의 위치와
현상을 실시간으로 확인할 수 있고 원인까지도 확인할 수 있어 최단 시간 내 복구가 가능합니다.
현상을 실시간으로 확인할 수 있고 원인까지도 확인할 수 있어 최단 시간 내 복구가 가능합니다.
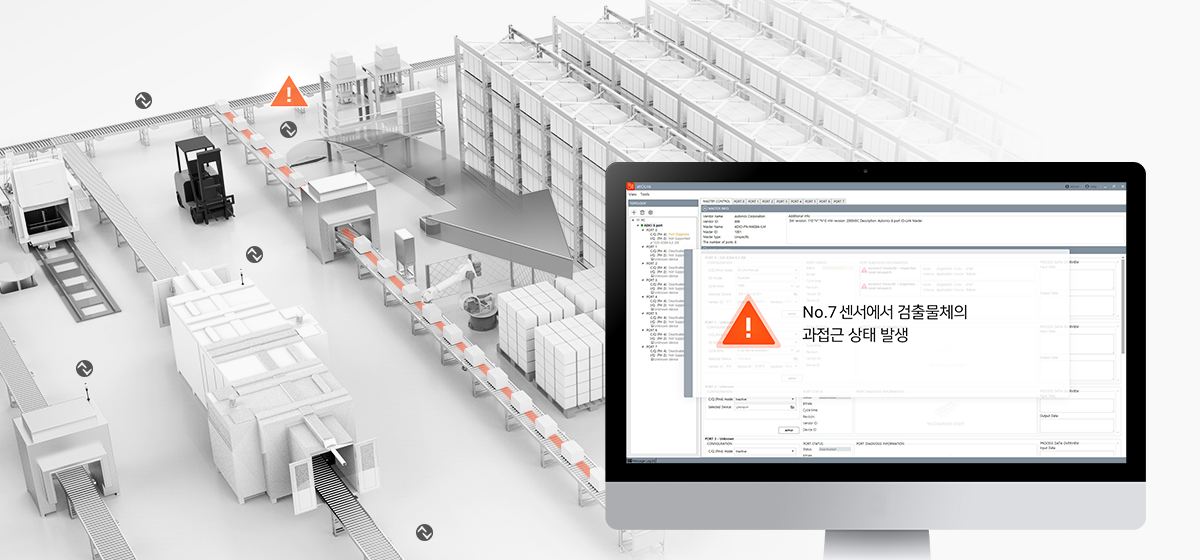
센서의 개별 ID로
이상 센서의 위치와 원인을
빠르게 파악 가능 !
이상 센서의 위치와 원인을
빠르게 파악 가능 !
※ 상기 이미지는 이해를 돕기 위한 예시입니다.
실시간 모니터링으로 예지보전
센서의 경우, ON/OFF 신호 뿐만 아니라 센서의 사용 시간, 단선 감지, 통신 상태 등의 진단 데이터를 확인할 수 있습니다.
이런 이유로 부품의 마모, 진동 등으로 인한 센서의 파손이나 오검출 등을 예측할 수 있으며 유지보수의 필요 여부 등을 확인할 수 있습니다.
이런 이유로 부품의 마모, 진동 등으로 인한 센서의 파손이나 오검출 등을 예측할 수 있으며 유지보수의 필요 여부 등을 확인할 수 있습니다.


IO-Link 통신으로
얻을 수 있는 정보
얻을 수 있는 정보

Process Data
디바이스와 마스터 간에 주기적으로
전송되는 일반적인 정보
전송되는 일반적인 정보

Service Data
모델 번호, 시리얼 번호, 오류 메시지, 유지보수
경고 메시지 등 장치 자체에 대한 정보
경고 메시지 등 장치 자체에 대한 정보

Event Data
전압, 카운팅 사이클 등 예방 정비지원을 위해
장치에 입력하거나 장치에서 읽을 수 있는 정보
장치에 입력하거나 장치에서 읽을 수 있는 정보
간편한 파라미터 설정 가능
센서의 IO-Link 파라미터값 및 설정 역시 소프트웨어를 통해 간편하게 변경할 수 있습니다.
센서 교체 시 마스터가 가지고 있는 IO-Link 파라미터를 그대로 데이터 스토리지(Data Storage) 기능을 사용하여
추가 설정 없이 센서를 바로 교체할 수 있어 간편하고 편리한 사용이 가능합니다.
센서 교체 시 마스터가 가지고 있는 IO-Link 파라미터를 그대로 데이터 스토리지(Data Storage) 기능을 사용하여
추가 설정 없이 센서를 바로 교체할 수 있어 간편하고 편리한 사용이 가능합니다.
데이터 스토리지(Data storage)란,
센서의 데이터 스토리지 리스트 파라미터의 설정 값을
마스터의 저장 공간(포트)에 저장하거나, 마스터의 저장
공간(포트)에 저장된 데이터 스토리지 리스트의 설정값을
센서에 다운로드하는 기능
마스터의 저장 공간(포트)에 저장하거나, 마스터의 저장
공간(포트)에 저장된 데이터 스토리지 리스트의 설정값을
센서에 다운로드하는 기능

IO-Link 통신 Application
공수절감
- 센서 개별 ID를 일괄 확인할 수 있어 센서 오접속 및 미접속, 설치 오류 등과 같은 공수 절감이 가능합니다.
-
1생산 라인 내 센서 설치 오류 발생
-
2센서의 개별 ID 확인으로 설치 오류 센서 확인 용이
-
3교체 및 정상적인 가동 가능
예지보전
- 기계 부품의 마모나 분진 등으로 인한 이상징후가 나타나기 전에 데이터가 전달되어 문제 발생을 미연에 방지할 수 있습니다.
-
1생산 라인 내 센서의 수광량 감소 문제 발생
-
2실제 현장을 찾아 수광량 감소 원인 파악 및 보수 작업 실시
-
3정상적인 가동 가능
다운타임 감축
- 이상 센서와 현상에 대한 데이터가 실시간으로 전달되어 센서의 위치와 원인을 쉽게 확인할 수 있어 신속한 유지보수로 인한 다운타임 감축이 가능합니다.
-
1현장 내 이상 센서 발생
-
2이상 센서의 위치와 이상 원인에 대한 파악 가능
-
3보수 작업으로 정상적인 가동 가능
※ 상기 이미지는 이해를 돕기 위한 예시입니다.